FAQ - Frequently Asked Questions:
Common Treatments to Yarns, Fabrics, Tapes and Sleeves
When yarns are manufactured, the producer will often apply oils, starches, waxes, or lubricants to the yarns.
These lubricants are necessary to prolong the life of the production machinery, especially for weaving or knitting.
In many cases, untreated tapes, sleeves and fabrics will satisfy all the end use requirements of the customer, however, for some applications further treatment may be necessary. To achieve best performance with some resins, tapes are cleaned using cleaning coupling agents (silanes). On narrow electrical grade tapes, acrylic finishes are applied to the tapes to enhance performance. A summary of treatments available:
Heat-cleaned: Tapes are placed in ventilated ovens and the temperatures are gradually increased to approximately 750° F. Starch oil
lubricants are slowly vaporized until the fabric is clean. The resulting tape is white.
(9383): Tapes are oven treated at approximately 400° F. Starches are partially converted to carbon. The starch oil lubricants
partially vaporize and the tape changes color to brown
Finish 111: Tapes are exposed to a temperature of 450° F. Tape color becomes golden brown. The lubricants partially vaporize
and the starches caramelize
Cold-cleaned: Tapes are cleaned in a water bath using scouring agents and enzymes
Multi-functional silane: This treatment is also called S910, A174, Z6020 and A1100. The silane used is 3-(Methacryloxy)
propyltrimethoxysilane. This silane is specified for polyester resin systems, but is also effective in
epoxy systems. Epoxy resin users sometimes specify 3-glycidoxypropyltrimethoxysilane. This is referred
to as S920, A187, and Z6040. This treatment is suitable for fabrics treated with phenolic resins.
Weave-set: A latex resin is applied to tapes to lock the weave or knitted stitch and improve stability. The finish is transparent
.
Starched: Tapes are coated with PVA to make the tape stiffer and improve dimensional stability. Customers that sew the
glass tapes often specify a starched finish. The PVA treatment is stable at high temperatures.
Finish 5: This is a pigmented acrylic coating on the tape. The color is yellow.
Finish 10: A clear acrylic coating on the tape
.
Polyurethane: This finish may be clear or pigmented. Black pigment is added to provide UV protection for high performance
fibers – e.g. Kevlar, Technora.
Vermiculite: Applied to finished products to enhance temperature range and abrasion resistance.
Calendered: Pressed under high pressure and heat. Laminated tapes and fabrics are often calendered with adhesive.
Edge-coated: Application of a resin on the edge of rolls of narrow fiberglass tapes. Improves efficiency in wrapping rods and coils.
May be applied to either untreated or treated tapes.
Graphite: Application of graphite disbursed in acrylic binder to fiberglass tapes
.
Water-repellent: Water-repellent finish is applied to tape in an aqueous bath. May be applied to either heat-cleaned or cold-cleaned tape.
Resin-compatible Yarns (RCY): The fiber producer applies a polymeric lubricant to yarns that is compatible with epoxy, urethane,
phenolic, and polyester resins. These yarn finishes do not need to be removed from the fabric.
Water-activated Urethane Resin Coating: Tapes are coated with custom-formulated resins that harden when exposed to moisture.
Very strong composite structures are possible with this technology. Coated rolls are
sealed in foil, waterproof pouches to maintain resin stability
Colored Glass Fiberglass: Yarns can be colored using a propriety process. Some colors are available that are stable up to 700°F.

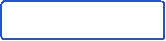
Share this page.....
1/18